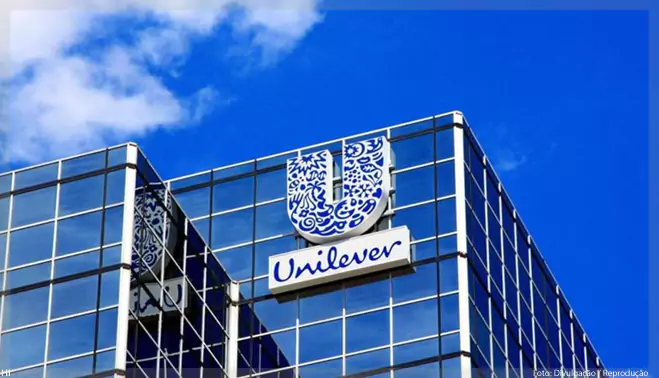
Five Ways Unilever’s Beauty & Wellbeing factory in Tinsukia, India, has been recognized by the World Economic Forum (WEF) as an End-to-End Value Chain Lighthouse site, marking a milestone in manufacturing innovation.
This achievement reflects the site’s exemplary use of cutting-edge technology, especially AI, to enhance efficiency, sustainability, and responsiveness. As the eighth Unilever site to join WEF’s Global Lighthouse Network, Tinsukia’s transformative journey provides a model for integrating Fourth Industrial Revolution (4IR) technologies at scale.
The WEF’s Global Lighthouse Network celebrates manufacturers utilizing advanced technologies such as AI, cloud computing, the Internet of Things (IoT), and factory automation to achieve financial, operational, and sustainability breakthroughs. With over 50 digital initiatives implemented across its supply chain, Tinsukia exemplifies the future of smart manufacturing. Below, we explore five key ways this site has scaled up AI to drive remarkable results.
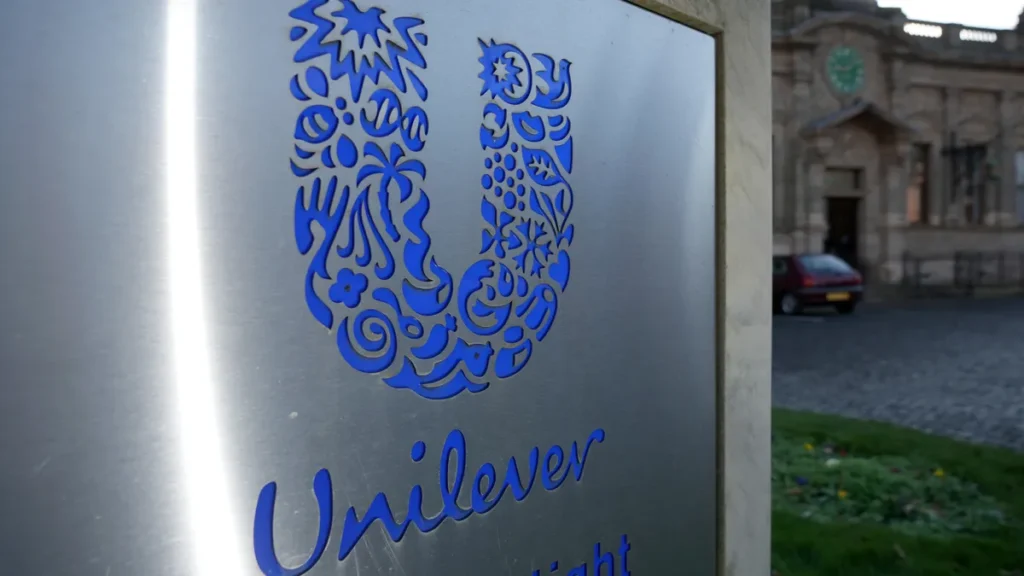
1. Rapid Changeovers for E-Commerce Readiness
The e-commerce sector’s rapid growth demands swift and efficient manufacturing processes to meet increasing consumer expectations for instant delivery.Five Ways Unilever’s Tinsukia has addressed this challenge by implementing an AI-powered vision system that maps product features and identifies anomalies in real time. This innovation enables rapid one-click changeovers when transitioning production lines between different products. The result? An 85% reduction in changeover times, enabling faster product availability and improved responsiveness to market demands.
This capability has been critical in ensuring that Unilever’s products, such as those under its iconic brands like Dove and Vaseline, reach consumers quickly without compromising quality or efficiency.
2. Superior Product Quality Through Data and Insights
Tinsukia employs generative AI-enabled consumer insights to elevate product quality. By analyzing large datasets of consumer feedback with 97% accuracy, the site can rapidly identify areas for improvement and implement changes. This data-driven approach has led to a 73% improvement in customer satisfaction scores and a 21% reduction in manufacturing defects.
Through the use of large language models, the site gains actionable insights from consumer data, ensuring that products not only meet but exceed consumer expectations. These insights are turned into improvements in real time, reinforcing Unilever’s commitment to delivering superior products.
3. Enhancing Workforce Productivity and Skills
Five Ways Unilever’s Tinsukia factory has embraced AI to optimize workforce productivity while fostering employee development. A newly developed AI-powered workforce allocation tool dynamically assigns employees to high-priority production lines based on their skills and experience. This tool also identifies skill gaps and provides targeted training to upskill employees.
As a result, labour productivity at the site has increased by nearly 400%. The initiative not only enhances operational efficiency but also empowers employees to take on more specialized roles, contributing to their professional growth. Unilever’s investment in its workforce underscores the company’s belief in the symbiotic relationship between human expertise and digital innovation.
4. Accelerating Sustainable Packaging Innovation with Digital Twins
Five Ways Unilever’s has set an ambitious goal to reduce virgin plastic use by 40% by 2028. The Tinsukia site is contributing significantly to this effort through the adoption of digital twin technology. By creating a virtual replica of the factory, the team can simulate, test, and monitor sustainable packaging options before implementing them in the physical environment.
This approach has dramatically increased the speed and scale of sustainable packaging trials. The site has reduced the time required for trials by 84%, increasing the number of annual trials from two in 2019 to 30 in 2023. These efforts have resulted in a 21% reduction in virgin plastic use at the site,Five Ways Unilever’s showcasing the potential of AI to drive meaningful progress toward sustainability goals.
5. Real-Time Demand Planning with AI
Tinsukia’s manufacturing operations produce over 5.4 billion units annually for renowned brands like Pond’s, Dove, and Vaseline. To meet the dynamic demands of consumers, the site has implemented an AI-enabled digital planning ecosystem that analyzes more than 10,000 product combinations using over 300 features. Five Ways Unilever’s This system ensures production aligns with real-time demand signals, enabling ultra-rapid e-commerce delivery.
The results have been transformative. The site has achieved a 92% reduction in the frozen period for production line schedules—from 14 days to just one day. Five Ways Unilever’s This improvement has enhanced speed to market, increased market responsiveness, and reduced finished goods inventory by 16%. Additionally, the ability to predict consumer demand has improved by 35%, further solidifying Tinsukia’s position as a manufacturing powerhouse.
A Model for Sustainable and Inclusive Growth
Five Ways Unilever’s Tinsukia’s success extends beyond technological advancements. Its digital transformation has created jobs and opportunities in the surrounding community, including the launch of a digital braille lab to support inclusivity and skill development among local professionals. Five Ways Unilever’s In collaboration with technology partners, the factory has extensively upskilled its workforce, with 23% of employees now redeployed as digital line leaders. This initiative highlights the site’s commitment to empowering individuals and fostering a culture of continuous learning.
“Five Ways Unilever’s Tinsukia is the third site in India and in our Beauty & Wellbeing business to achieve WEF’s Lighthouse recognition. Its digital transformation is a powerful example of how we’re scaling AI across our supply chain to accelerate growth for our business now and into the future,” says Biswaranjan Sen, Beauty & Wellbeing Chief Product Supply Officer.
Factory Leader Kunwar-Apoorva Singh adds: “We’re pleased that technology has not only had a positive impact on our business, it’s also benefited our employees and local community. Five Ways Unilever’s Our digital factory transformation has created jobs and opportunities around this remote location, including the launch of a digital braille lab to create an inclusive pool of skilled local professionals.”
Scaling AI for a Future-Ready Supply Chain
Tinsukia’s recognition as a WEF Lighthouse site underscores Unilever’s commitment to leveraging AI and other 4IR technologies to build a future-ready supply chain. By seamlessly integrating cutting-edge digital tools with human ingenuity, the site is setting a benchmark for the industry. From enhancing product quality to accelerating sustainable packaging innovations, Tinsukia demonstrates how AI can drive measurable impact across financial, operational, and environmental dimensions.
As Unilever continues to expand its digital capabilities, the lessons from Tinsukia’s transformation will undoubtedly serve as a blueprint for other sites worldwide. This milestone reaffirms the power of AI to create a smarter, faster, and more sustainable future for manufacturing.